Ball Mill Machine Particles Size Range Of Recive And Gives

MILLING &ANALYSIS OF PARTICLES AUTUMN 2010
In our lab course, we will work with a centrifugal ball mill. The feedstock can be filled up to 10 mm and will be milled to particles of about 1 μm. The mill consumes a maximum
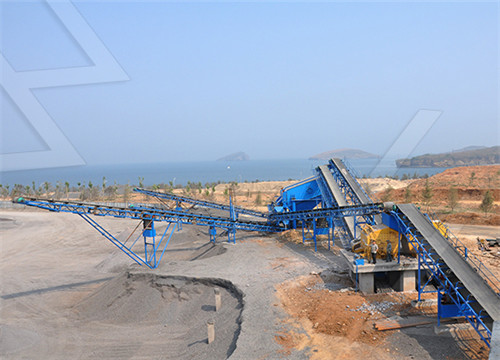
(PDF) Grinding in Ball Mills: Modeling and Process Control
2012年6月1日Besides particle size reduction, ball mills are also widely used for mixing, blending and dispersing, amorphisation of materials and

What particle size range does ball mill grinding produce?
2016年12月22日Key properties of grinding media are size, density, hardness, and composition. Size: The smaller the media particles, the smaller the particle size of the
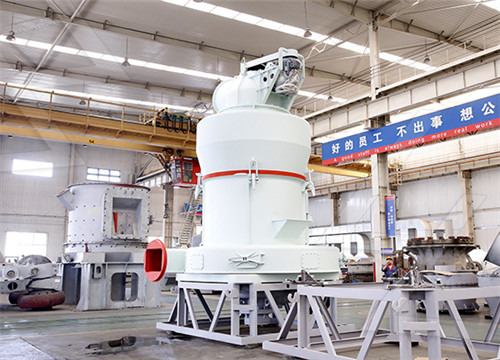
Particle Size Distribution of Grinding Mill Products
2019年4月27日The charge was composed of equal portions of -7 +8 and -8 +10 size fractions. The ball load was 455 stainless steel balls one inch

The Effect of Ball Size Diameter on Milling Performance
An investigation was conducted to determine the effect of the ball diameter sizes on milling operation. A laboratory size ball mill was used with ball media of sizes 10 mm, 20 mm

Nano Grinding MillsMethods — When Smallest is Best
Justin Klinger, Jun 16, 2022 9:22:00 AM. Nanonization (sometimes also called nanoization) refers to the processes used to make particles that range in size from 1 nanometer
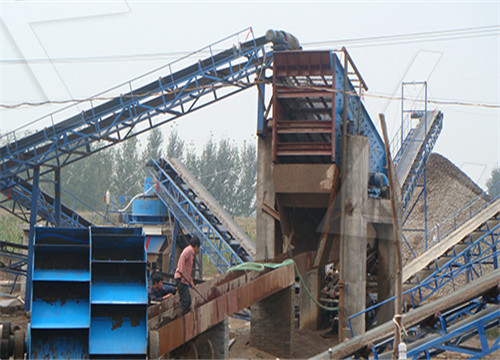
ball mill machine particles size range of recive and gives
Ball milling has been shown to be an effective mechanical process to decrease particle size to the sub-micron size domain for a wide range of energy related materials 16,17

ball mill machine particles size range of recive and gives
2021年5月7日2015 11 11 First order and second order breakage rate of coarse particles in ball mill grinding 269 If the total mass load in the mill is at particle size i=1 single
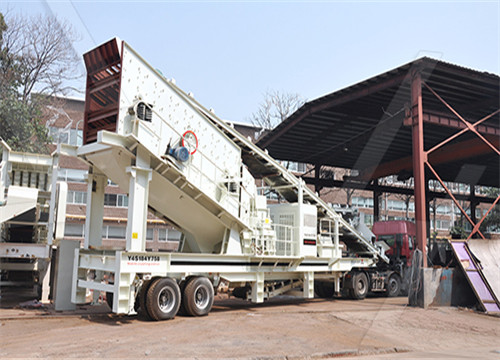
ball mill machine particles size range of recive and gives
Nov 05, 2010 0183 32 good evening viking ran across your video on the ball mill and was wondering how it worked out i got a tumbler free at a yard sale a while, Ball Mill Home

Effect of ball and feed particle size distribution on the milling
2018年6月1日Mass fraction of each of selected six size classes vs. time for J = 20%, 20 mm ball size and feed size = -1700 + 850 μm. In order to find an optimal solution using the Attainable region technique only three size classes need to be used. These are the feed, intermediate and fine size classes.
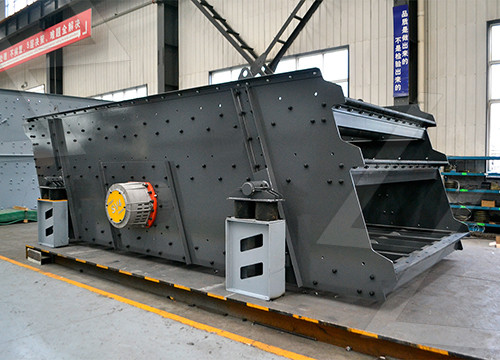
Study of Microstructure and Mechanical Properties of Ball
2021年4月23日The morphology of SiC particles after 40-h of milling time, as observed under FESEM is shown in Fig. 2. The particles are greatly fractured and larger fraction of nano size particles in 40-h milled samples are observed, this could be due to excess work hardening and enhancement of brittleness of the particles by milling [21, 22].

MILLING &ANALYSIS OF PARTICLES AUTUMN 2010 ETH Z
In our lab course, we will work with a centrifugal ball mill. The feedstock can be filled up to 10 mm and will be milled to particles of about 1 μm. The mill consumes a maximum power of 100 W. (Do not assume the mill produces 100W of comminution power) In Fig. 6 the parts of the mill are described. A B C Figure 6: Centrifugal ball mill
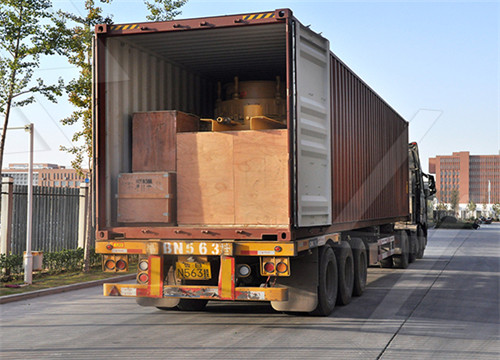
Review on Titania Nanopowder- Processing and Applications
Ball milling is one of the effective mechanical milling processes and the The decreasing of particles size depends on the powder-to-ball weight ratio. Fig.1. Commercial Ball Mill image. Figure is adapted from [11]. Ball mill image is shown in Fig.1. Ball mills are the main equipment in grinding industry and (size range from 0.05 mm to 3

Particle Size Distribution of Grinding Mill Products
2019年4月27日The charge was composed of equal portions of -7 +8 and -8 +10 size fractions. The ball load was 455 stainless steel balls one inch in diameter, having a total weight of 30 kg. The particle size distribution was observed after 20, 40, 60, 80, 100, 150, 200 and 300 ball mill revolutions.
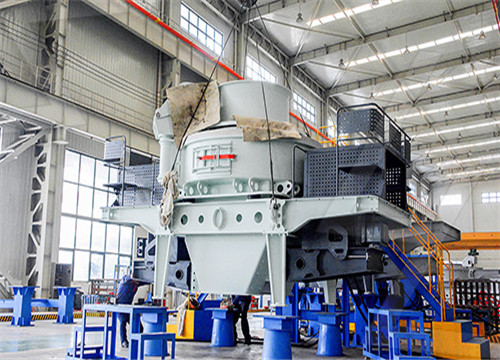
How can I mix two different ceramics powders via ball milling
2015年4月17日I want to mix two different ceramics powders using ball milling machine. In the same time I need not any reduction or reducing in particles size. How can I do that? I have some...
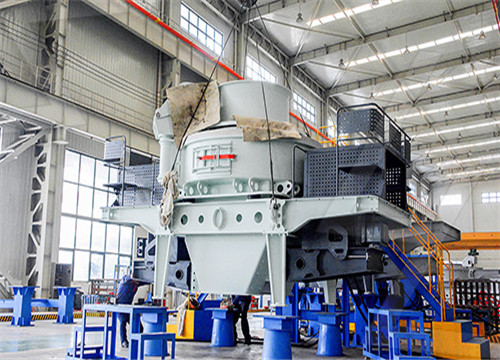
The Effect of Ball Size Diameter on Milling Performance
An investigation was conducted to determine the effect of the ball diameter sizes on milling operation. A laboratory size ball mill was used with ball media of sizes 10 mm, 20 mm and 30 mm respectively. Quartz was the material used to perform the experiment and was arranged into 3 mono-sizes namely -8 mm +5.6 mm, -4 mm +2.8 mm and-2

ball mill machine particles size range of recive and gives
Ball milling has been shown to be an effective mechanical process to decrease particle size to the sub-micron size domain for a wide range of energy related materials 16,17 and is commonly used in preparation of electrode materials. In principle, ball milling is a simple and scalable process, which results in variation of the stoichiometry

ball mill machine particles size range of recive and gives
Roller Mill Machine Particles Size Range Of Recive And . Roller Mill Machine Particles Size Range Of Recive And Gives 250tph river stone crushing line in Output size : 140250mm Production capacity : T/H Copper ore beneficiation plant Iron Ore Beneficiation Plant 20TPH vertical mill for limestone desulfurization in power plant

ball mill machine particles size range of recive and gives
The grinding charge in a ball mill consist of cast or forged steel balls. These balls are fed together with the feed and consequently ball mills can be in operation for months without stopping. The ball size is often in the diameter range of 20-75 mm. The biggest size is chosen when the mill is used as a primary grinding mill.
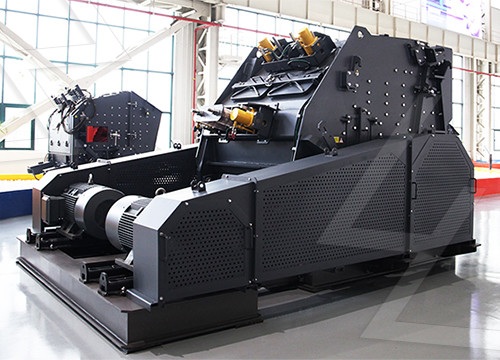
Nano Grinding MillsMethods — When Smallest is Best
Nano Grinding Mills: Tiny Particles Can Be a Big Deal Justin Klinger, Jun 16, 2022 9:22:00 AM Nanonization (sometimes also called nanoization) refers to the processes used to make particles that range in size from 1 nanometer (nm) to 100 nm. Many biological processes are nanoscale. In the human body, hemoglobin measures about 5.5 nm in
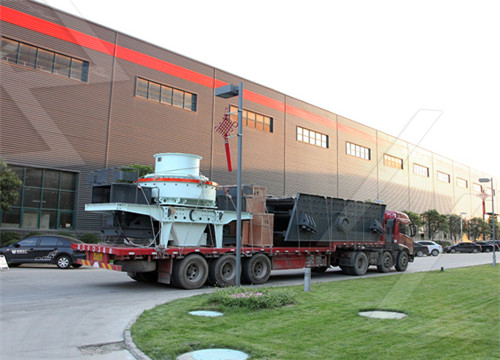
Membranes Free Full-Text Fabrication of Thin Film Composite
2022年9月27日Figure 2 a shows the typical morphology of nanozeolites obtained after the ball milling process. More than half of the particles were in a size range of 75 nm to 125 nm with a size distribution as presented in the supplementary Figure S3.

Ball milling: a green technology for the preparation and
Further research on the effects of milling conditions (i.e. ball-to-cellulose mass ratio, milling time, ball size and alkaline pre-treatment) on the morphology of the prepared nanocellulose derivatives was undertaken by the group of Wang. 22,23 More in detail, they found out that the size of the milling balls has an impact on the formation of
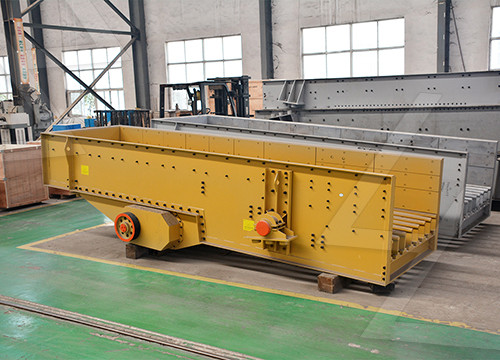
Properties of biomass powders resulting from Open
2021年10月19日Process parameters of the ball mills to yield powders with a 20-µm median particle size. RBM=rotary ball mill; mpl=stirred ball mill; VBM=vibratory ball mill. Particle size analysis and agglomeration PSD was measured using a Mastersizer 2000 laser diffraction granulometer (Malvern, UK). Several procedures were employed.
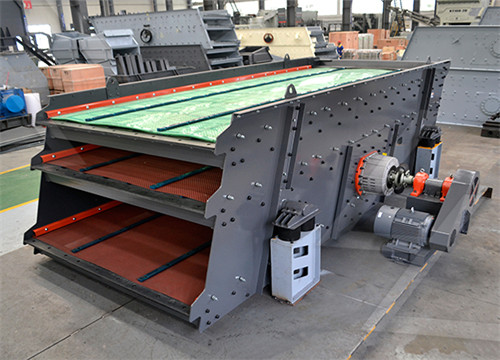
Ball milling: a green technology for the preparation and
Further research on the effects of milling conditions (i.e. ball-to-cellulose mass ratio, milling time, ball size and alkaline pre-treatment) on the morphology of the prepared nanocellulose derivatives was undertaken by the group of Wang. 22,23 More in detail, they found out that the size of the milling balls has an impact on the formation of
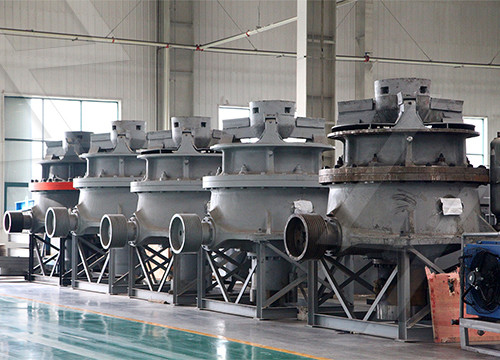
Effect of ball and feed particle size distribution on the milling
2018年6月1日Mass fraction of each of selected six size classes vs. time for J = 20%, 20 mm ball size and feed size = -1700 + 850 μm. In order to find an optimal solution using the Attainable region technique only three size classes need to be used. These are the feed, intermediate and fine size classes.

MILLING &ANALYSIS OF PARTICLES AUTUMN 2010 ETH Z
In our lab course, we will work with a centrifugal ball mill. The feedstock can be filled up to 10 mm and will be milled to particles of about 1 μm. The mill consumes a maximum power of 100 W. (Do not assume the mill produces 100W of comminution power) In Fig. 6 the parts of the mill are described. A B C Figure 6: Centrifugal ball mill

Study of Microstructure and Mechanical Properties of Ball
2021年4月23日The morphology of SiC particles after 40-h of milling time, as observed under FESEM is shown in Fig. 2. The particles are greatly fractured and larger fraction of nano size particles in 40-h milled samples are observed, this could be due to excess work hardening and enhancement of brittleness of the particles by milling [21, 22].

Ball Mill Ball Mills WetDry Grinding DOVE
DOVE small Ball Mills designed for laboratories ball milling process are supplied in 4 models, capacity range of (200g/h-1000 g/h). For small to large scale operations, DOVE Ball Mills are supplied in 17 models, capacity range of (0.3 TPH 80 TPH).

Particle Size Distribution of Grinding Mill Products
2019年4月27日The charge was composed of equal portions of -7 +8 and -8 +10 size fractions. The ball load was 455 stainless steel balls one inch in diameter, having a total weight of 30 kg. The particle size distribution was observed after 20, 40, 60, 80, 100, 150, 200 and 300 ball mill revolutions.

Minerals Free Full-Text Comparison of Particle Shape, Surface
2023年1月8日For conventional ball milling, a laboratory-scale stainless steel ball mill (without lifter) having a dimension of 200 mm × 200 mm and a volume of 6283 cm 3 with a 0.37 kW variable speed motor was utilized ( Figure 4 b).

The Effect of Ball Size Diameter on Milling Performance
An investigation was conducted to determine the effect of the ball diameter sizes on milling operation. A laboratory size ball mill was used with ball media of sizes 10 mm, 20 mm and 30 mm respectively. Quartz was the material used to perform the experiment and was arranged into 3 mono-sizes namely -8 mm +5.6 mm, -4 mm +2.8 mm and-2
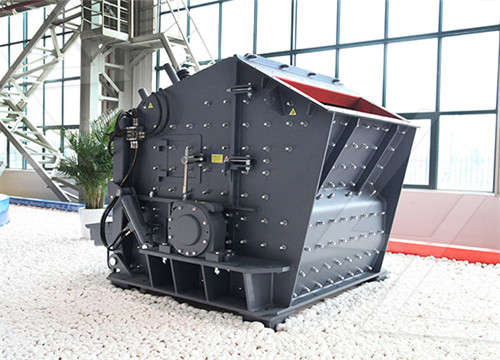
ball mill machine particles size range of recive and gives
Ball milling has been shown to be an effective mechanical process to decrease particle size to the sub-micron size domain for a wide range of energy related materials 16,17 and is commonly used in preparation of electrode materials. In principle, ball milling is a simple and scalable process, which results in variation of the stoichiometry

ball mill machine particles size range of recive and gives
The grinding charge in a ball mill consist of cast or forged steel balls. These balls are fed together with the feed and consequently ball mills can be in operation for months without stopping. The ball size is often in the diameter range of 20-75 mm. The biggest size is chosen when the mill is used as a primary grinding mill.
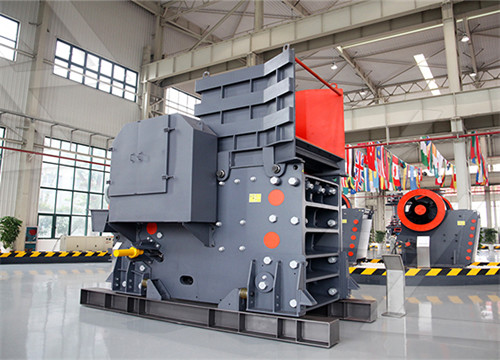
How can one select ball size in ball milling and how much material
2015年1月31日Ball size depends on initial size of charge and ranges from 10mm-150mm dia. For particular material and initial size the ball size must be optimized. Please refer the link below and see...

Properties of biomass powders resulting from Open
2021年10月19日Process parameters of the ball mills to yield powders with a 20-µm median particle size. RBM=rotary ball mill; mpl=stirred ball mill; VBM=vibratory ball mill. Particle size analysis and agglomeration PSD was measured using a Mastersizer 2000 laser diffraction granulometer (Malvern, UK). Several procedures were employed.
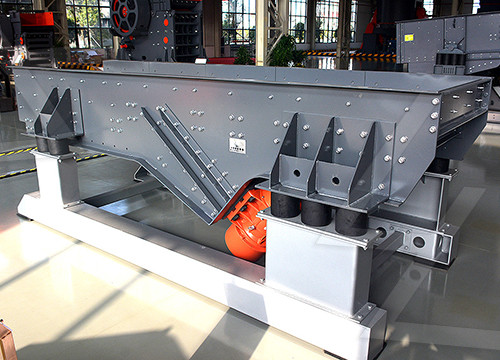
DVKLQFRQFUHWH iopscience.iop
[7, 11, 12]. High energy ball milling is one of the machines developed to grind micro particles to the Nano size. 3. Nano waste materials Many researchers have investigated the waste materials in Nano size, which are prepared by grinding in Laos Angeles machine and/or high energy ball mill [13, 14]. The presence of significant amount of silica

Ball Mill Explained saVRee
For both wet and dry ball mills, the ball mill is charged to approximately 33% with balls (range 30-45%). Pulp (crushed ore and water) fills another 15% of the drum’s volume so that the total volume of the drum is 50% charged. Pulp is usually 75% solid (crushed ore) and 25% water; pulp is also known as ‘ slurry ’.